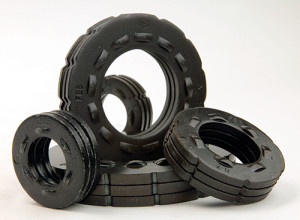
Direct Tension Indicators (DTIs) ensure accurate tension of bolts, help prevent leaks and eliminate fugitive emissions.
ARE DTIs REALLY WORTH IT?
Could something that costs 10 cents actually guarantee better bolt tension accuracy than your company’s designer?
This question sounds ridiculous to many people since they blindly trust their designer’s torque calculations. Unfortunately, the calculations they rely on to get proper tension may have been determined 10 years earlier by someone that cannot predict all bolt conditions.
In many instances, a designer can only predict some, but not all, of the conditions a bolt may encounter when out in the field. These conditions, which can include such things as rust and lubricant break down, are known as “K” Factor and can make accurate torque calculations nearly impossible to predict.
“The prediction of “K” Factor in a controlled environment is accurate to a point but once fasteners are taken out into the field, their conditions can deteriorate dramatically,” according to Rich Brown, Vice President of Quality and Engineering at TurnaSure LLC, a maker of a load indicating washer, also known as a Direct Tension Indicator (DTI).
“The relationship between torque and tension gets worse and worse and the spread between what you want and what you get gets wider and wider,” Brown emphasizes.
In tests, a new bolt without lubricant achieves half the prescribed tension as a new bolt with lubricant torqued to the same tension, Brown explains. In addition, a bolt that’s exposed to the elements for a month and torqued to the same perimeters as the new bolt with lubricant only achieves a quarter of the proper bolt load tension. If critical joints are not properly tensioned, a disaster could result.
“When you use a DTI, the DTI could care less what condition your fasteners are in,” Brown says. “Whether bolts are brand new. Whether they are in a dry condition. Whether they have been exposed to the elements. DTIs don’t care.”
Load indicating washers have been around since the early 60s and are highly accurate load cell washers with raised protrusions that collapse to a specified gap as the bolt is tensioned/tightened. With DTIs, the proper gap is verified by a “go/no go” feeler gauge. Once the specified gap is attained, proper tension has been achieved to the appropriate standard.
“The engineers are discovering that the old fashioned way of using torque to get proper tension is a faulty method, and it is not reliable,” explains Brown. “The most simple and cost effective solution is a DTI, which can range from a small one that costs 10 cents to a large that could cost $20. Even at the high end, the cost is miniscule compared to the potential impact of an under-tensioned bolt.”
Training takes less than a minute. “The learning curve is quick” compared to other significantly more expensive methods of measuring bolt tension, like ultrasonic extensometers, according to Brown.
“It is the cost effectiveness and simplicity of the DTI that is getting people’s attention. DTIs are very cheap insurance to ensure that every bolt is properly tensioned.”
Until around 10 years ago, load indicating washers were used exclusively in structural steel applications, such as constructing buildings and bridges. Since then, companies like TurnaSure have made them viable for the automotive, petrochemical and wind turbine industries.
“Most recently, the largest DTI we produced was a 2 ¾-inch DTI for a large oil company used on a platform in the Gulf. They (the company) required over a half of million pounds of tension,” says Brown.
Load indicating washers are finding more popularity in industries where critical joint failure could cause a large-scale disaster, such as oil and gas.
TurnaSure produces DTIs in a variety of materials, including stainless steel and are available in sizes ranging from ¼ to 3 inches. They are also available in several different finishes, with many offering corrosion protection.
“All we need is the diameter of the fastener, the size and the grade, and if we don’t already have it on the shelf, we can develop it for the customer,” Brown says. “We can also modify the DTI to the customer’s specification so the DTI will achieve the exact specification of tension the customer wants.
DTI’s keep their accuracy in very cold and very hot conditions and have been used on the Alaskan Pipeline in sub zero weather and in high temperature applications as hot as 1200 degrees.
So, the next time you want to quickly and accurately ensure your bolts have been tensioned accurately, the low cost and efficiency of using DTIs just may be the insurance policy your project needs.
FASTORQ is the exclusive distributor of DTIs to the oil and gas industry. To learn more about how DTIs can help ensure tension accuracy in your bolted joints, go to http://www.fastorq.com/products/direct-tension-indicators or watch a video about just how well they work at http://www.youtube.com/watch?v=fUVEAzqRcpE.
AUG
About the Author:
Lisa Raynor-Keck is the Marketing Communications Specialist at FASTORQ. She earned her degree in journalism from the University of Central Florida and gained her early writing experience at newspapers in Michigan and Tennessee. In addition to her press positions, Lisa's work portfolio includes experience as a freelance writer, political campaign ad designer and public relations professional. She also has experience working as an editor and writer for the technology division at Middle Tennessee State University and an articles editor for the Navy's former online military lifestyle website Lifelines. Lisa is currently studying to earn her M.A. in corporate communication at Austin Peay State University.